- Sealing materials
- Coating materials
- Conductive pastes
- Insulating pastes
- Solders
- Adhesives
- Printed circuit boards
- Circuit substrates
Introduction Examples
Can be used across a wide range of fields, for wide-ranging applications, and a diverse range of materials
Field Examples
-
Electronic Materials
-
Chemical Materials
- Carbon nanotubes
- Carbon fibers
- Carbon blacks
- Ceramics
- Urethane resins
- Silicone resins
- Acrylic resins
-
Energy Materials
- Fuel batteries
- Electrode materials
- All-solid-state batteries
- Secondary batteries
- Solar panels
-
Automobile-related Materials
- EVs
- Batteries
- Fuel batteries
- Tires
- Greases
- Adhesives
- Heat radiating materials
- Paints
-
Medical Materials
- 3D shaping
- Dental materials
- Endoscopes
-
Semiconductor-related Materials
- Ceramic members
- Adhesives
- Machine parts
- Transfer machine parts
-
Imaging-related Materials
- Organic EL displays
- Liquid crystal displays
- LED displays
-
Cosmetic Materials
- Foundations
- Lipsticks
- Nail polishes
- Eyeshadows
- Hair colorings
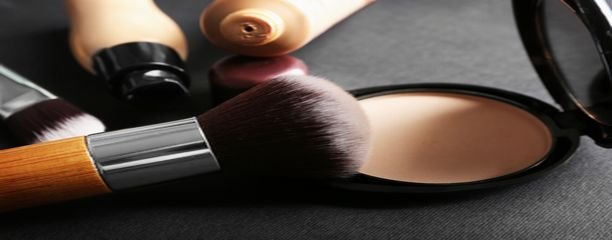
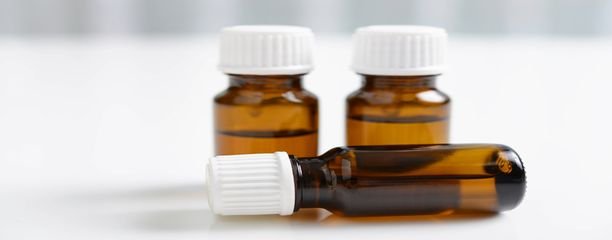
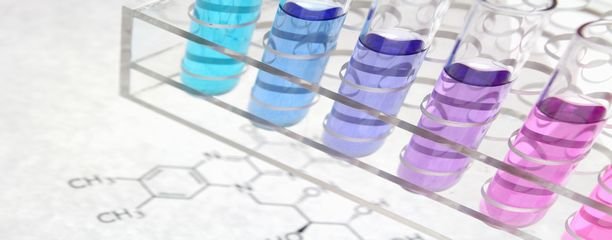
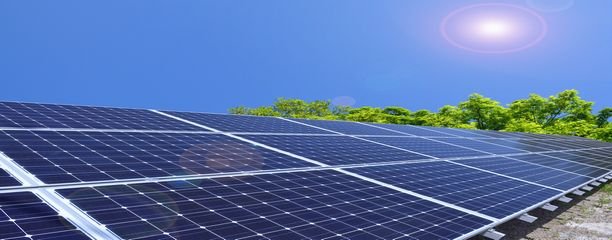
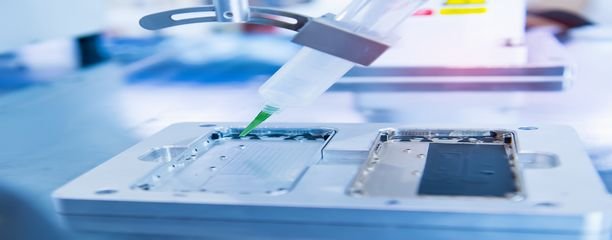
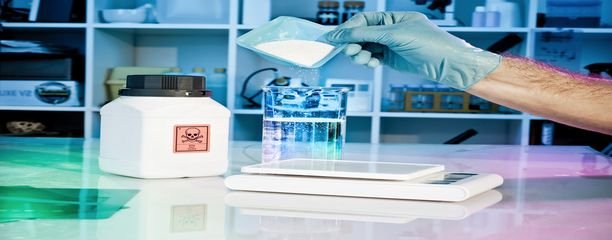
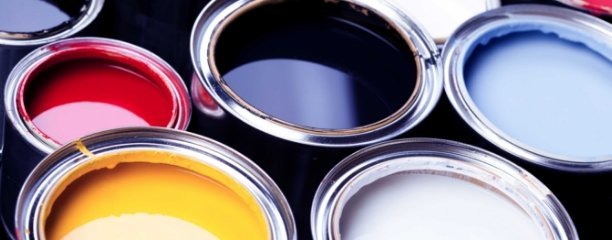
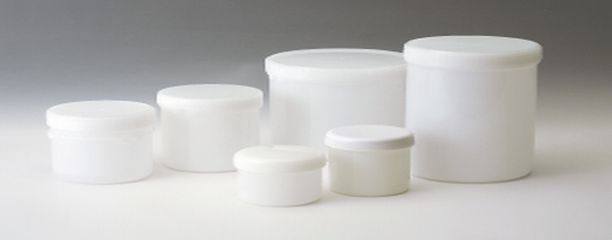
Inquiry / Brochure Request
For inquiries about our service and products, contact us from the link by clicking on the button below.
* You will be redirected to a page on another domain managed by us.
We have made available a brochure with detailed information about Kakuhunter and catalogs for each product model.
* You will be redirected to a page on another domain managed by us.
Developed and distributed by:
SHASHIN KAGAKU CO., LTD. Product Company
Weekdays 9:00 a.m. ~ 5:00 p.m. (closed on Saturdays, Sundays, and holidays)