- 封止材
- コーディング材
- 導電ペースト
- 絶縁性ペースト
- はんだ
- 接着剤
- プリント基板
- 回路基板
導入事例
CASE STUDIES
カクハンターは、マーケットにおける技術の進歩とともに、撹拌・分散・脱泡の精度を飛躍的に向上させています。
よって、さまざまな産業分野において、用途を問わず、幅広い材料の撹拌脱泡にご利用いただけます。
分野例
-
電子材料
-
化学材料
- カーボンナノチューブ
- カーボンファイバー
- カーボンブラック
- セラミック
- ウレタン樹脂
- シリコーン樹脂
- アクリル樹脂
-
エネルギー材料
- 燃料電池
- 電極材
- 全個体電池
- 二次電池
- ソーラーパネル
-
自動車関連材料
- EV
- バッテリー
- 燃料電池
- タイヤ
- グリース
- 接着剤
- 放熱材料
- 塗料
-
医療系材料
- 3D造形
- 歯科材料
- 内視鏡
-
半導体関連材料
- セラミックス部材
- 接着剤
- 装置部品
- 搬送装置部品
-
映像関連材料
- 有機ELディスプレイ
- 液晶ディスプレイ
- LEDディスプレイ
-
化粧品材料
- ファンデーション
- 口紅
- マニキュア
- アイシャドー
- ヘアカラー
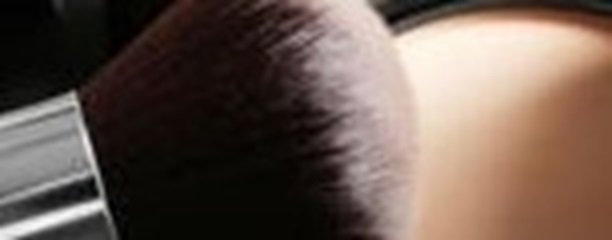
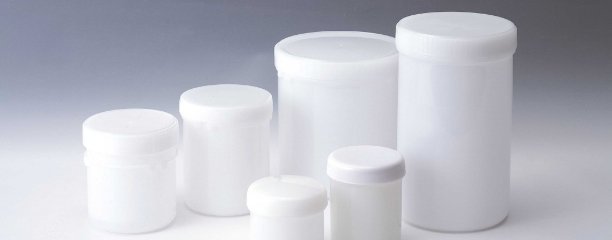
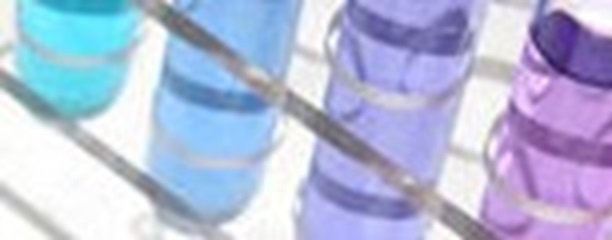
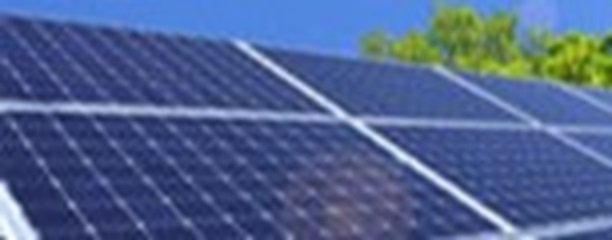

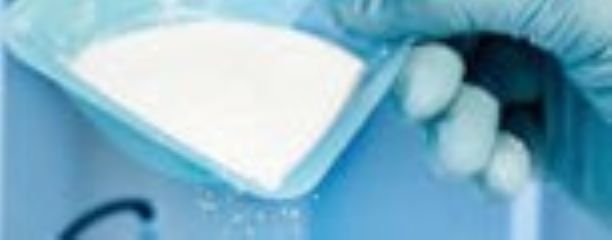
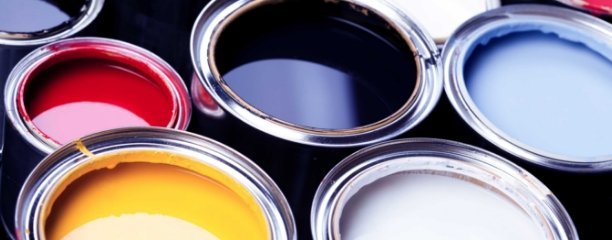
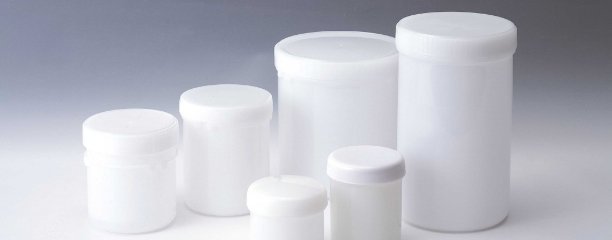
1
お問い合わせ・
資料お取り寄せ
開発・販売
西日本
077-566-1208
平日 9:00~17:00(土日・祝休み)
東日本
03-5361-6688
平日 9:00~17:00(土日・祝休み)